Reaction Vessel

Charmi Engineering's Reaction Vessel
The Perfect Solution for Precision and Efficiency in Chemical Processing
Reaction vessels are an indispensable component of modern industries, playing a crucial role in facilitating various chemical processes. Designed to ensure safe, efficient, and precise reactions, these vessels are engineered to meet the demanding requirements of industries such as chemicals, pharmaceuticals, food processing, and more. Whether for heating, cooling, mixing, or chemical synthesis, reaction vessels are vital for achieving optimal process outcomes.
At Charmi Engineering, we specialize in manufacturing high-quality reaction vessels tailored to meet your unique industrial needs. Built with superior-grade materials and advanced technology, our reaction vessels deliver unmatched durability, efficiency, and performance. Explore why reaction vessels are the ideal choice for your operations and how they contribute to seamless and productive processes.



Applications of Reaction Vessels
Maintenance Tips for Reaction Vessels
Reaction vessels are extensively used for chemical synthesis, polymerization, crystallization, and other processes requiring precise temperature and pressure control.
A reaction vessel is a specialized container designed to hold chemical reactions under controlled conditions. These vessels are typically made from materials such as stainless steel (SS 304, SS 316) or other corrosion-resistant alloys, ensuring durability even in harsh environments. Reaction vessels are equipped with features such as jacketed designs, agitators, and temperature control systems to facilitate efficient heat transfer, mixing, and precise temperature regulation.
Reaction vessels are used in both batch and continuous processing setups, making them versatile for a wide range of applications. They can handle reactions involving high pressure, extreme temperatures, and sensitive materials, ensuring consistent results and maintaining the integrity of the chemical processes.
- Regular Cleaning: Periodically clean the vessel interior to prevent residue buildup.
- Inspect Components: Check seals, gaskets, and agitators regularly for wear and tear.
- Monitor Performance: Keep track of temperature, pressure, and mixing efficiency to identify potential issues early.
- Professional Servicing: Schedule routine maintenance with experts to ensure optimal performance.
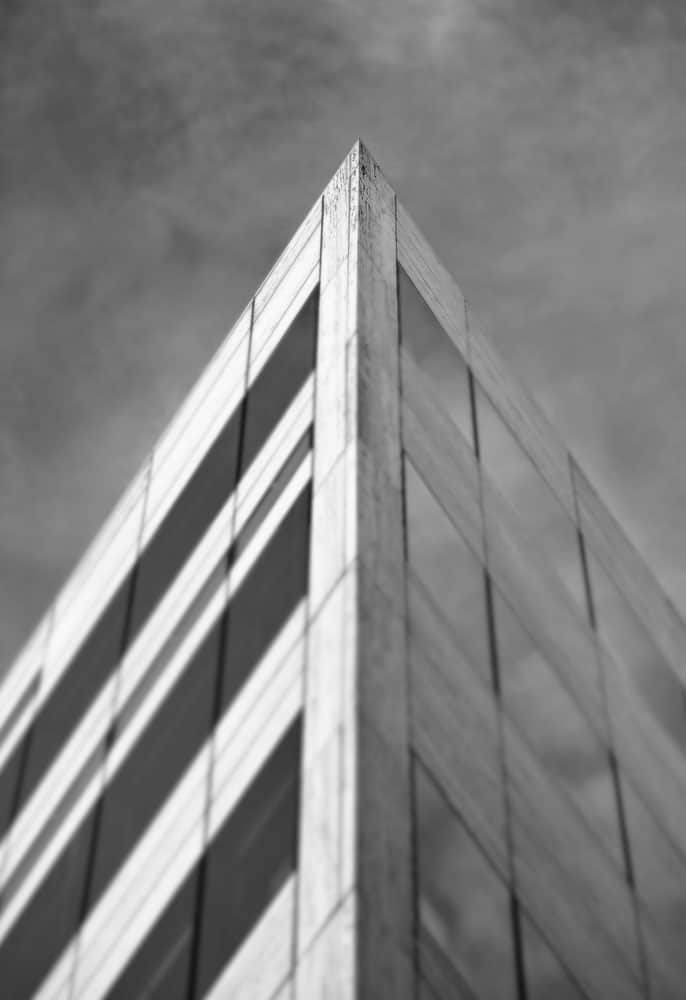
SPECIFICATIONS
Capacity : 2 M2 – 50 M2 Condenser
Materials : Chemicals / Oil
Weight : As Per Size
Material : MS / SS
Usage / Application : Heat / Cooling Transfer
INDUSTRIES WE SERVE
- Engineering & Structural Works
- Biotech & Pharmaceutical
- Chemical & Petrochemical
- Mechanical Piping & Utility
- Turnkey Based Project Equipment
- Customized Fabrication Works
Our Amazing Clients
Lorem ipsum dolor sit amet, consectetur adipiscing elit. Ut elit tellus, luctus nec ullamcorper mattis pulvina.
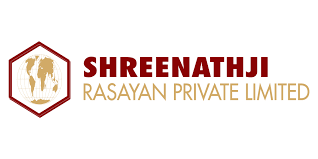
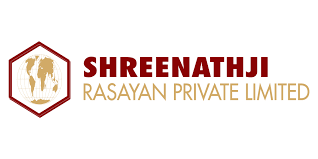
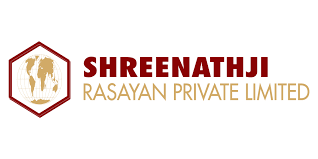
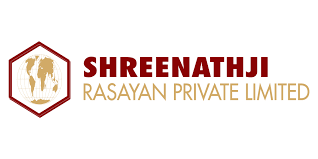